Production times halved thanks to additive manufacturing
The project, which stemmed from the company’s need to reach higher-performance production targets, was developed by ProM Facility, Trentino Sviluppo’s mechatronic prototyping and product development centre which, like Pulsar Industry, is based at Polo Meccatronica in Rovereto.
The arm-gripper system from Pulsar Industry grabs objects from a conveyor belt and places them precisely and quickly into a container. Gripping takes place by means of pneumatic suction cups positioned on the gripper, which hold the products and thus ensure the continuity of the handling process.
The production efficiency of the entire automated system is affected by action time. The work of reducing the masses and inertias involved made the robot faster, thus reducing the duration of the entire transport cycle.
The redesign and 3D printing of grippers
The robotic arm project is one of many examples of successful collaboration between Pulsar Industry and ProM Facility. In this specific case, the Rovereto-based company asked the mechatronic prototyping centre to print metal parts that needed quick modification.
This challenge was taken up by the Polo Meccatronica facility, which carried out a metal replacement job by proposing plastic models instead of steel, the original material, thus optimising production time and costs.
The new parts were 3D printed in Polyamide 12 (PA12), also known as Nylon 12, using HP Multi Jet Fusion (MJF) technology.
To reduce the masses and inertias of the grippers, ProM Facility followed a hybrid approach, combining FEM – Finite Element Method simulation with topological optimisation.
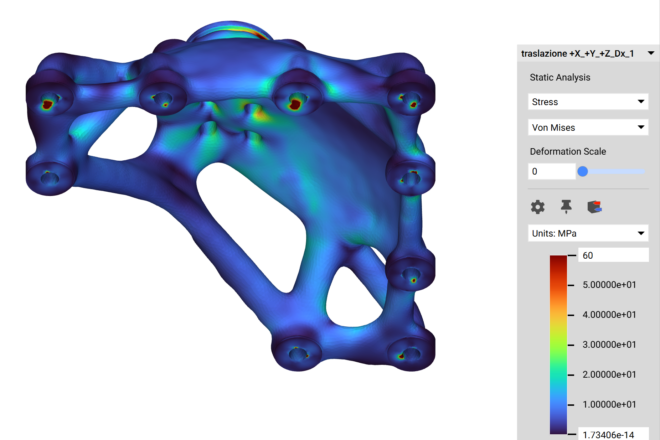
The new arm-gripper system from Pulsar Industry
During the redesign phase, the pipes carrying the vacuum to the suction cups were turned into the supporting structure of the gripper. This minimised the use of material and also improved the flow of air in the channels. Before this step, the vacuum tubes were outside the aluminium structure and all metal fittings were far from the rotational axis.
The end result has fully achieved the initial objective. As a result of the redesign work, the weight of the model has dropped from 1520 grams to 711 grams, and the torsional inertia has been greatly decreased compared to the starting situation.
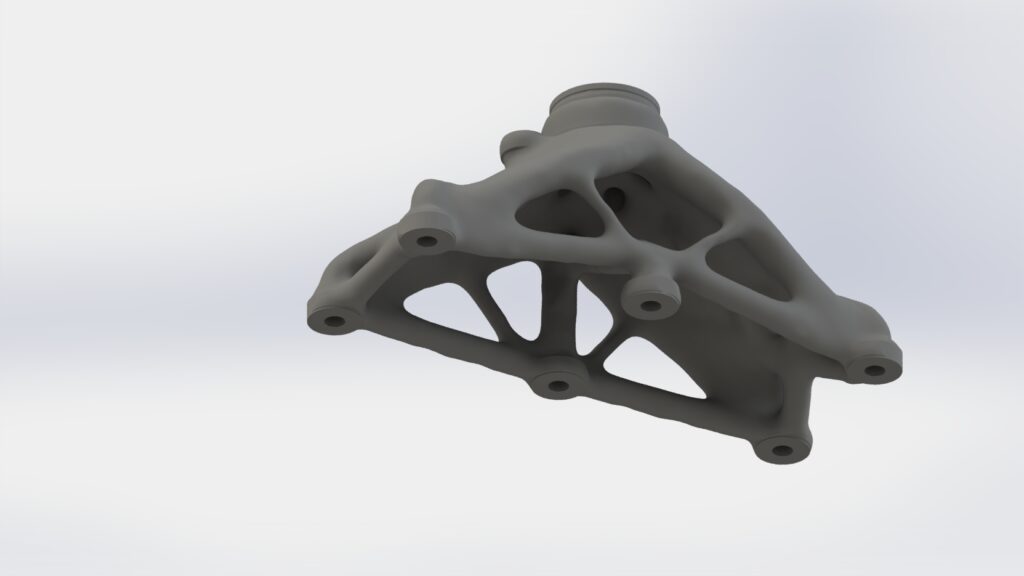