The Rovereto-based manufacturer of gearboxes and lift machines, in collaboration with the Department of Industrial Engineering and our prototyping centre, has initiated a project to study new technologies to reduce the use of these materials in the construction of gears. The experimentation, developed as part of the ‘Bronze Worm’ project financed by Fondazione Caritro, was illustrated during the ‘Sustainability in the Production of Mechanical Elements’ conference held on Wednesday, 9 April at the Polo Meccatronica venue.
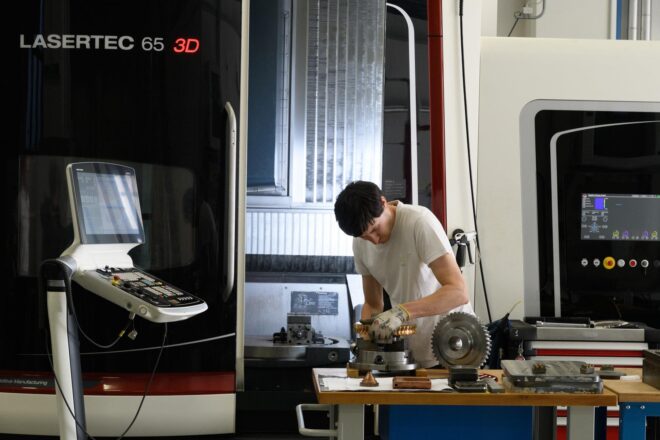
Instead of constructing the traditional sprocket wheels entirely from bronze, and thus be composed of 89% copper and 11% tin, they opted for new steel sprockets, coated with bronze on the tooth surfaces where the contact surface adaptation and seizure resistance of bronze are irreplaceable. The innovation was made possible thanks to the DMG MORI Lasertec 65 3D hybrid. This machine, present in the ProM Facility, combines milling with Directed Energy Deposition (DED). The resulting gears were further machined by Sicor to obtain the correct degree of finish and tolerances, then tested in the company’s workshops.
WATCH THE VIDEO
"This project could be revolutionary for all those components, such as gear wheels and plain bearings, which require large quantities of bronze when machined using traditional technologies. With the processes developed in the project, however, it is possible to significantly reduce their use, limited only to relative sliding parts. The same technology could also be used to extend the service life of worn components for which the original thickness of bronze is restored."
Prof. Matteo Benedetti (University of Trento), scientific head of the 'Bronze Worm' project
"This is a unique 3D printing technology that allows material to be deposited on an existing object. Instead of making them entirely of bronze, we made a supporting toothing out of steel, which is a more common, mechanically resistant, cheap and abundant material on the market. Then we coated them with bronze in the outermost and most superficial layer of the toothing"
Matteo Perini, Engineer, ProM Facility
"If this construction technique were to catch on, it could give as an additional benefit the possible increase in the degree of safety against gear slippage, which is highly appreciated in the vertical transport sector."
Marco Chemello, Engineer, Technical Director